University researchers analyze oxide films at atomic level to understand corrosion, which may lead to material improvements in the future.
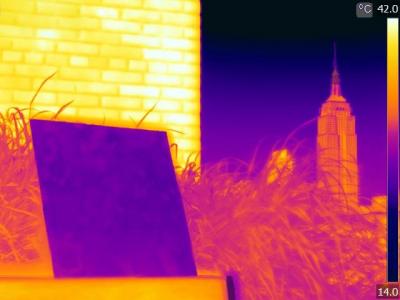
Perfecting PDRCWhile efforts have increased to phase out high-global warming potential hydrofluorocarbons and ramp up programs to improve air conditioning equipment efficiency to save energy and emit less greenhouse gasses, dependency on air conditioning will see a vast global increase in the next 30 years, necessitating alternative eco-friendly methods.1,2 One alternative to these energy-intensive cooling methods is passive daytime radiative cooling (PDRC), where a surface spontaneously cools by reflecting sunlight and radiating heat to the colder atmosphere. However, many recent PDRC design proposals are complex or costly and cannot be widely implemented or applied on rooftops and buildings, which have different shapes and textures.3 Building on previous research, researchers at Columbia Engineering have invented a high-performance exterior PDRC polymer coating with nano-to-microscale air voids that acts as a spontaneous air cooler and can be fabricated, dyed, and applied like paint on rooftops, buildings, water tanks, vehicles, and spacecraft—anything that can be painted. The research was published in the September 27, 2018 issue of Science.3,4 Keeping it CoolUp to now, white paints, which are inexpensive and easy to apply, have been the benchmark for PDRC.3 “While traditional white paints are indeed very reflective in the visible wavelengths, they are usually made using titania or zinc oxide (the same materials as in sunscreen), so they actually absorb UV light, which contains approximately 6% of the sun’s energy,” said Jyotirmoy Mandal, lead author of the study, in an interview with Innov8 Updates. “Moreover, often they also do not reflect the infrared part of sunlight, which contains approximately 50% of sunlight, so the total solar reflectance of paints is usually around 85%—even the 15% that is absorbed can heat roofs up under strong sunlight. In contrast, our PVDF coating has 96% to 99% solar reflectance, which minimizes heating by sunlight. As a result, it stays colder than the structures around it, and can even reach sub-ambient temperatures,” he said. Mandal stressed that a difference of 10% in reflectivity can mean a difference in solar heating by 120 watts /m2 roof area. He said that avoiding that heating, as the coating invented by the Columbia team does, can mean the difference between heating and cooling. The team comprised of Yuan Yang, assistant professor of materials science and engineering; Nanfang Yu, associate professor of applied physics; and Mandal used a solution-based phase-inversion technique that gives the polymer a porous foam-like structure. The air voids in the porous polymer scatter and reflect sunlight, due to the difference in the refractive index between the air voids and the surrounding polymer. The polymer turns white and thus avoids solar heating, while its intrinsic emittance causes it to efficiently lose heat to the sky.3 The challenges were how to get these normally transparent polymers to reflect sunlight without using silver mirrors as reflectors and how to make them easily deployable. The team decided to use phase-inversion because it is a simple, solution-based method for making light-scattering air-voids in polymers. Polymers and solvents are already used in paints, and the Columbia Engineering method essentially replaces the pigments in white paint with air voids that reflect all wavelengths of sunlight, from UV to infrared.3 A Coat of a Different ColorThe team also created colored polymer coatings by adding dyes and compared them to traditional paints for heat gain. In general, darker colors have less solar reflectivity, therefore, Mandal made note of their coating’s results using black as a ‘worst-case’ example. “Traditional black paints absorb not only the visible, but also the UV and infrared parts, so they have a total solar reflectance of 5%-10%. In comparison, our coating, while still black in the visible, has much higher reflectivity (40%-45%) across the total solar spectrum, and can stay significantly cooler,” Mandal said. He noted that similar results can be expected for other colors, but results would depend on the color. Keeping it CleanThe team used poly(vinylidene fluoride-co-hexafluoropropene), which is known to be resistant to weathering and fouling, but have yet to conduct long-term tests on their coating. Mandal said they expect the effects on performance to be no worse than on paints. He also noted that in extremely polluted settings, like factories, it is possible to protect the coating by adding a thin, smooth plastic film of the same polymer (or a different one) on top, which can be periodically washed to remove surface dirt. Yang, Yu, and Mandal are refining their design in terms of applicability, while exploring possibilities with different polymers and solvents. They are currently in talks with industry about next steps.3 References
|
|